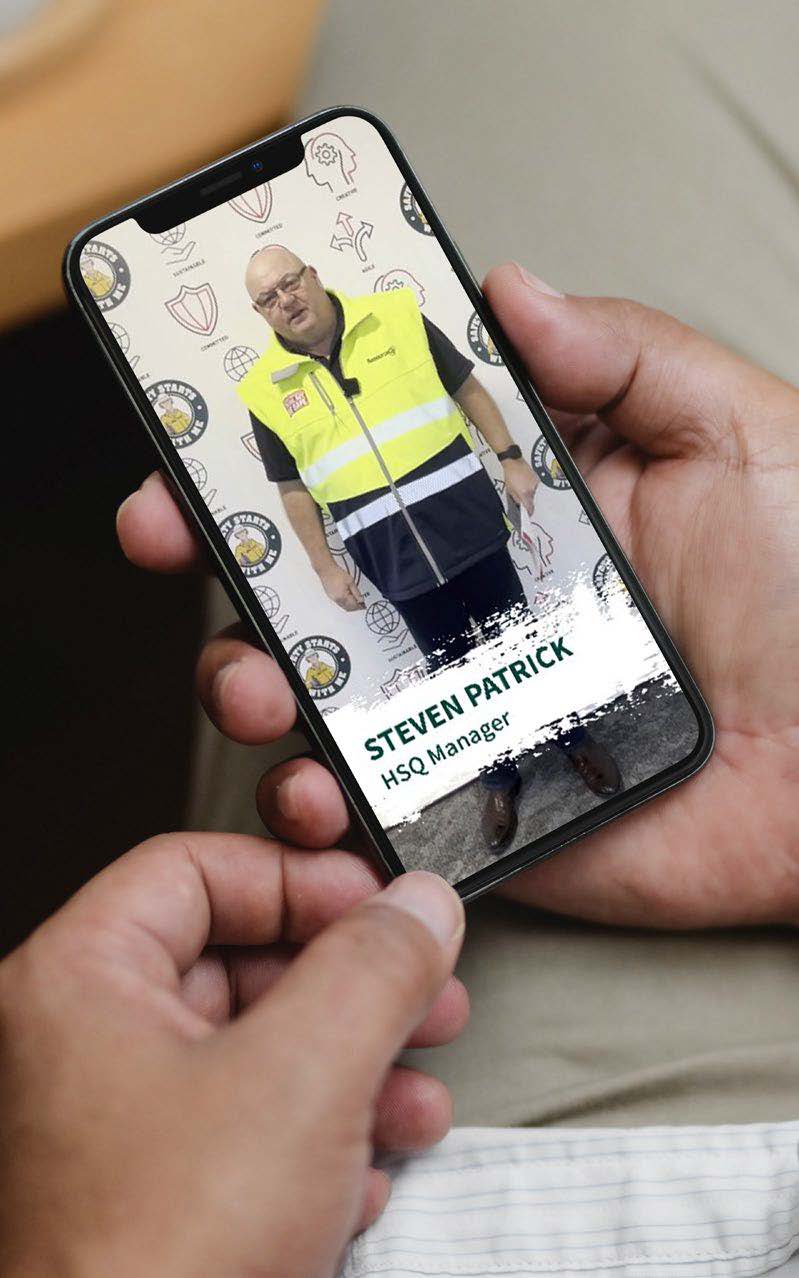
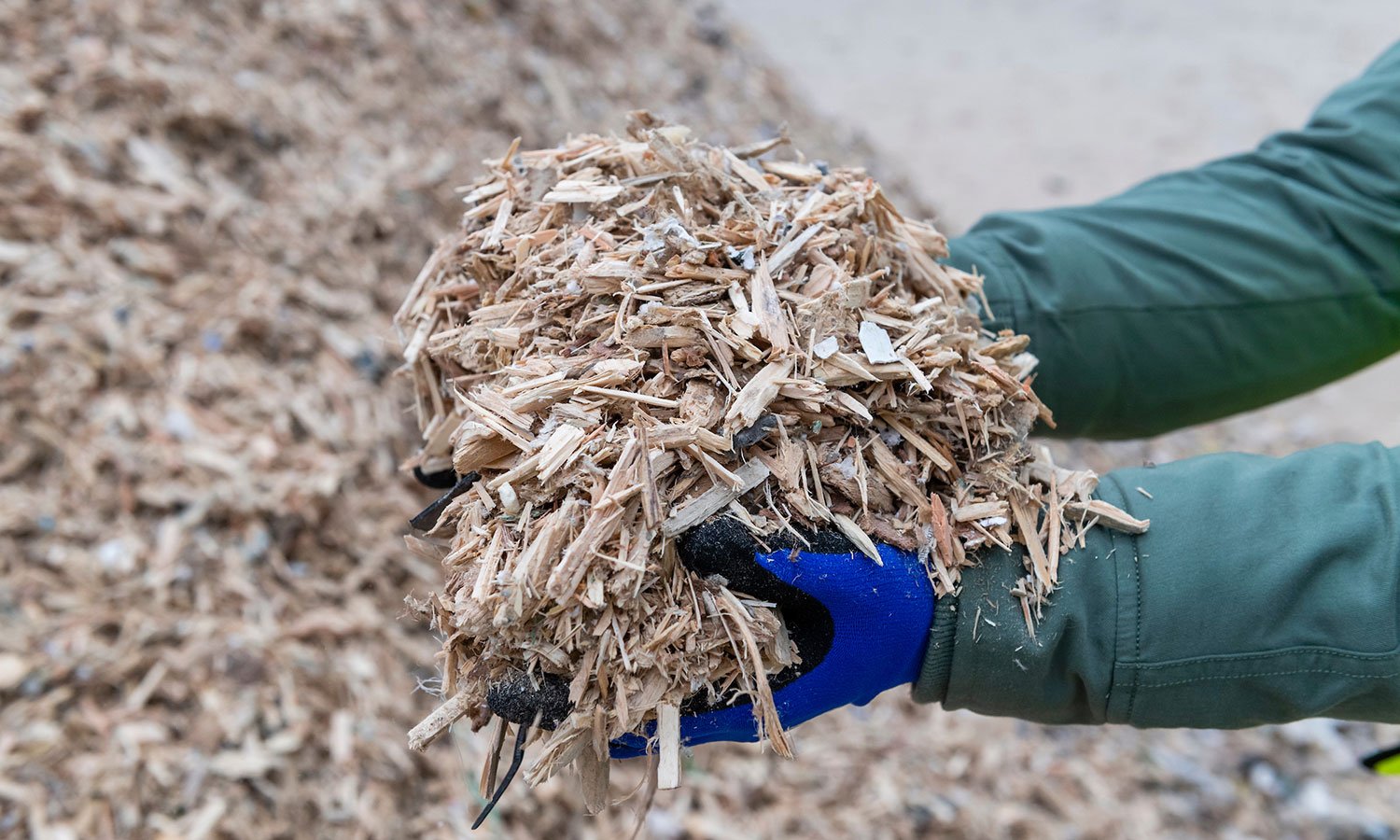
As governments and communities across the world grapple with the challenge of dealing with the mountains of waste produced through modern living, the need to grow existing; and establish new markets for the repurposing of waste is becoming ever more critical.
China’s decision to stop accepting rubbish from countries like Australia since the beginning of 2018 turned significant community and political focus to what countries do with their waste. What’s important within that debate, is that we are able to have a meaningful conversation about the very distinct differences between contaminated rubbish being dumped on foreign shores and legitimate high value recycled commodities, including waste to energy solutions, for which there is high global demand.
Encouragingly, the Council of Australian Governments (COAG) recently agreed to establish a timetable to ban the export of waste plastic, paper, glass and tyres, saying Australia needed to take responsibility for its own waste. Hand-in-hand with that decision is the need to continue to build Australia’s local recycling capacity, changing from a make, use and dispose model to the recovery, recycling and re-use of products to extract their maximum value. It’s in this space that opportunity abounds for Australia’s advanced waste to energy sector, which has a significant role to play in adding capability to the emerging global circular economy.
As an international leader in resource recovery and alternative fuels, ResourceCo has already repurposed 40 million tonnes of raw waste materials that would have otherwise found its way into landfill. The construction and demolition and commercial and industrial components of that waste is converted into energy, in the form of processed engineered fuel (PEF), using world-leading technology. PEF is a finished product that is generated from select dry non-recyclable materials, and not from municipal waste. For more than a decade, ResourceCo has been producing this ready-to-use alternative fuel source that replaces the use of fossil fuels, servicing well-established markets for high-energy users in both Australia and South-East Asia. The company continues to invest significantly in research and development, with its two Australian PEF plants producing a product that has a lower emissions profile and displaces millions of tonnes of fossil fuels at a lower price point, as well as abating hundreds of thousands of tonnes of CO2. While traditionally the product has been used in cement kilns in Australia, in Europe this fuel has been used in biomass boilers to produce lower cost, lower emissions heat and electricity for decades.
As demand and likewise opportunity for sustainable, environmentally sound energy solutions increases on the back of governments and communities looking for ways to conserve the earth’s limited resources, its vital that product quality is not compromised. The market for PEF is rapidly expanding both here and abroad because it offers a win-win solution to businesses grappling with increased regulation, while also crying out for cost-effective alternative energy solutions in the face of skyrocketing gas and electricity prices. PEF’s growing reputation as the ‘holy grail’ in sustainable energy production and its broadened scope of application for energy hungry businesses is attracting numerous new entrants into the market.
As the Australian leader in PEF production, we are encouraged by its uptake as an alternative energy source but advise those seeking alternative fuel options to do their homework. Not all PEF is created equal and inferior products will most certainly deliver inferior results, both in terms of energy production, energy continuity and environmental outcomes. The key factors that influence PEF quality are energy content of the fuel, ash, moisture, particle size and key chemicals including chlorine and sulphur.
The critical first element to ensure a high-quality end product is sourcing the right mix of raw waste materials and then forensically processing the waste to ensure adverse chemicals and inert materials are meticulously removed. This is achieved through a combination of mechanical, pneumatic, magnetic, eddy current, optical and human processes. Without the right equipment and expertise, the production process yields an inferior PEF with higher ash and moisture content and less of the high calorific content which reduces energy yield. The final imperative in the processing of PEF is to ensure the final fuel is sized to the correct particle dimensions as the wrong sized final fuel can cause significant problems for the end users’ equipment. It takes experience to producing a fuel to specification, every time, for years.
To safeguard against a lower quality fuel, the best advice is to ask questions about a potential supplier’s experience, ensure you agree a comprehensive specification which matches your business needs and seek out independent product testing through a laboratory with National Association of Testing Authorities (NATA) accreditation.
The future for PEF is enormous. Its ability to harness the energy value of material currently going to waste in landfill sites is unrivalled. More than 20 million tonnes of waste is still landfilled in Australia each year – the energy content in this waste alone is equivalent to half of all natural gas used in Australian industry. PEF presents a cost-effective, circular solution to the generation of sustainable baseload energy, helping to address the complex and expensive issues of waste management and energy production. In realising the opportunities at hand, we must draw on the best science, research and commercial experience to deliver the best outcomes – both for industry and the environment.