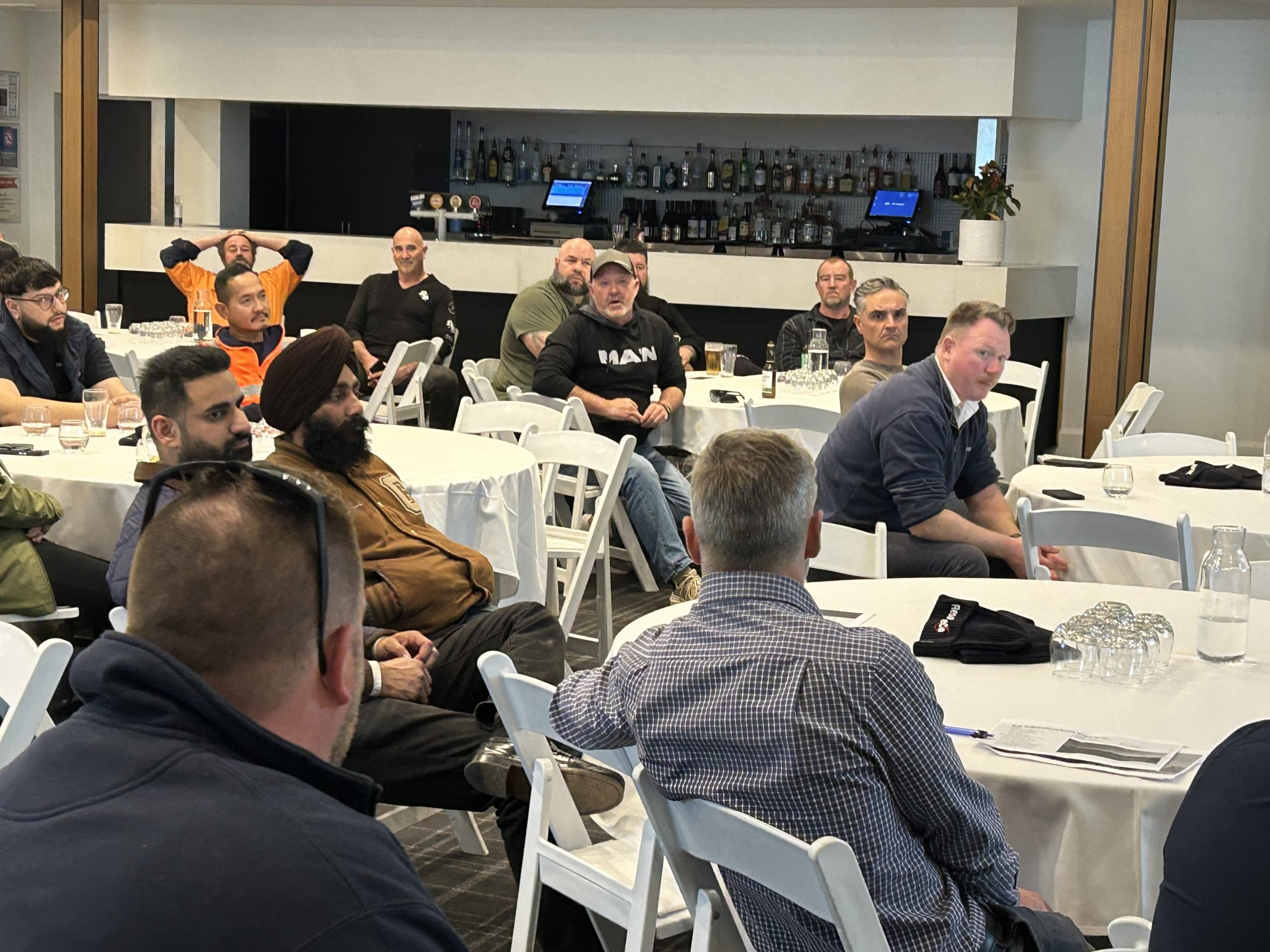
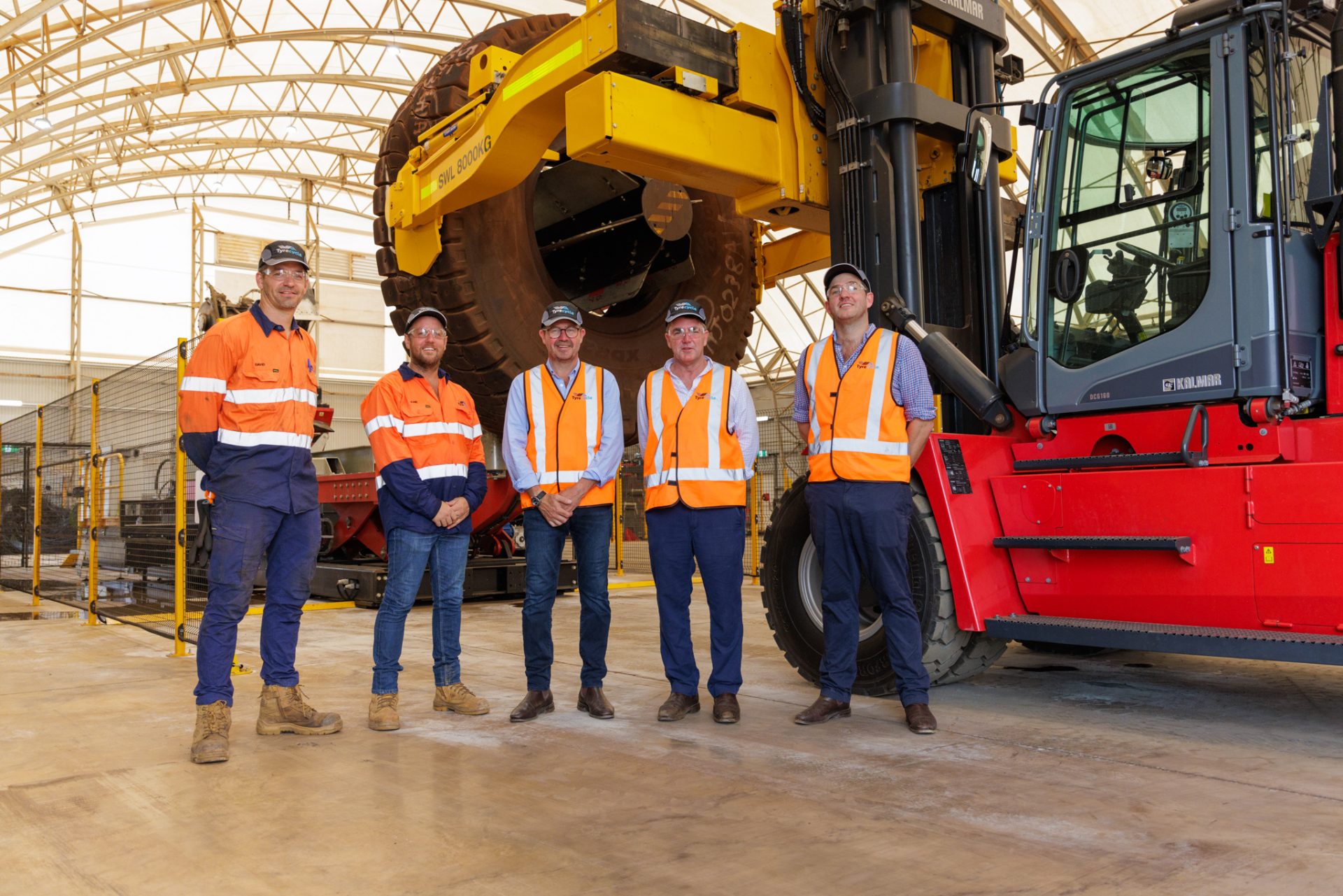
End-of-life, off the road (OTR) mining tyres in Western Australia’s Pilbara region will now be recycled instead of buried, thanks to Tyrecycle opening an Australian first, purpose-built facility in Port Hedland.
Tyrecycle’s new facility will have the capacity to process over 30,000 tonnes of OTR mining tyres annually, providing an efficient mine-to-processing service, and enhancing sustainability credentials for operators in one of the world’s busiest mining regions.
Tyrecycle Chief Executive Officer, Jim Fairweather, said opening the facility in such a busy mining area will make it easier than ever to deliver sustainable outcomes for end-of-life mining tyres and conveyor belts.
“As a market leader we are proud to see this first facility of its kind in the country up and running, revolutionising OTR mining tyre recycling will ensure that these massive tyres are no longer seen as a disposal challenge but instead a resource for the achievement of better sustainable outcomes,” he said.
“Transporting end-of-life OTR mining tyres can be a challenge, which is why it was really important that we base this new facility as close to the source of the waste as we can.
“It’s been a five-year journey to get to this point, which is a great step forward for Port Hedland, the biggest export terminal in the world.”
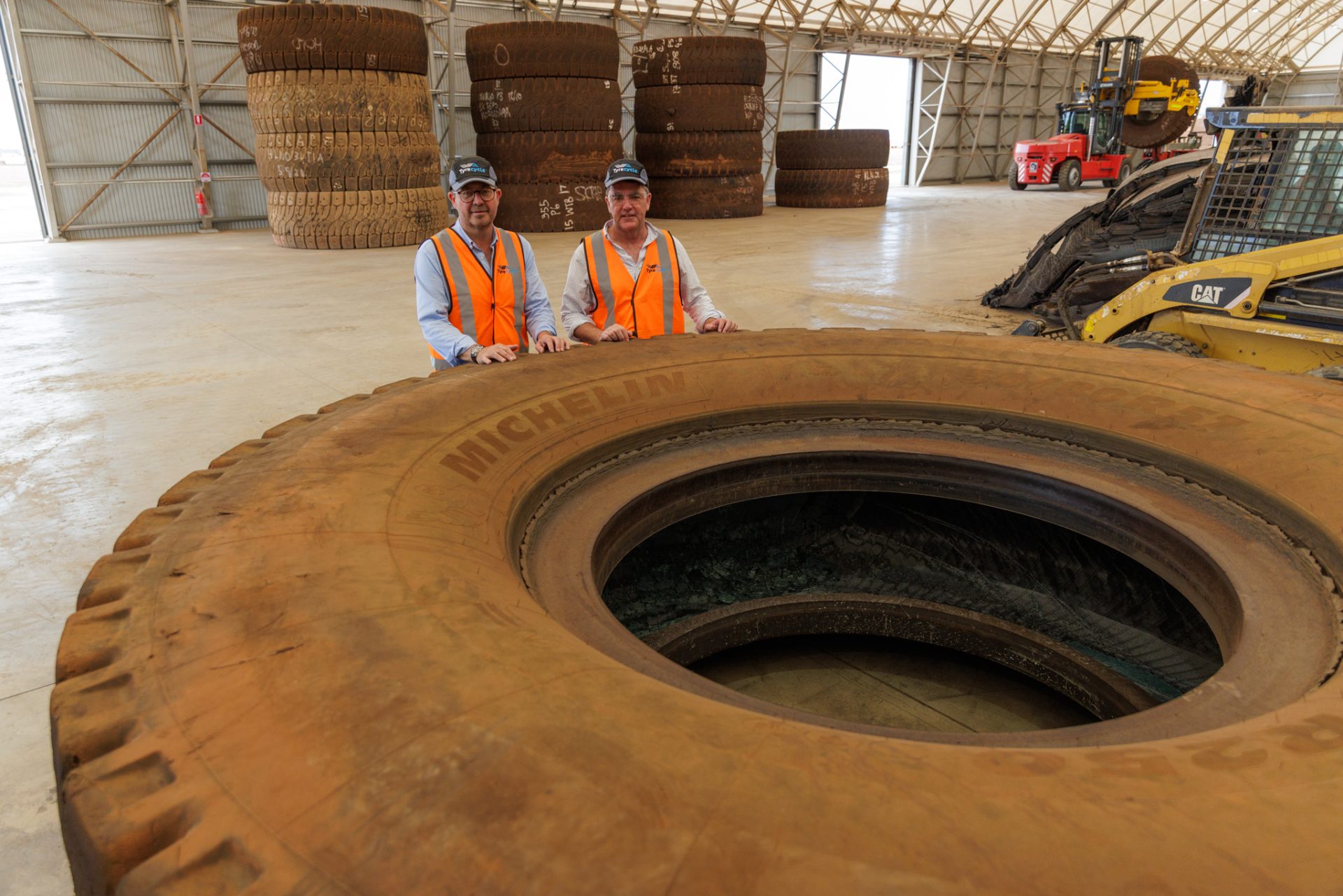
Fairweather credited the mining industry for its willingness to work with Tyrecycle in driving the charge for more sustainable outcomes for its end-of-life OTR tyres.
“Mining companies recognise the importance of managing their waste streams responsibly, and we’re here to work alongside them to deliver more sustainable outcomes,” he said.
“They know that responsible management of end-of-life tyres is an important part of best practice operations, this new facility means burying these tyres in pit, will soon be a thing of the past.
“The mining sector has been eager for a solution to end-of-life OTR mining tyre management, and with the establishment of this new facility, Tyrecycle is providing them that solution.
“The outcomes our new plant provides are outstanding, we’ll be able to demonstrate significant traceability and chain of custody confidence, along with carbon benefits to our customers as a result of partnering with us for the sustainable management of their tyres and conveyor belts.”
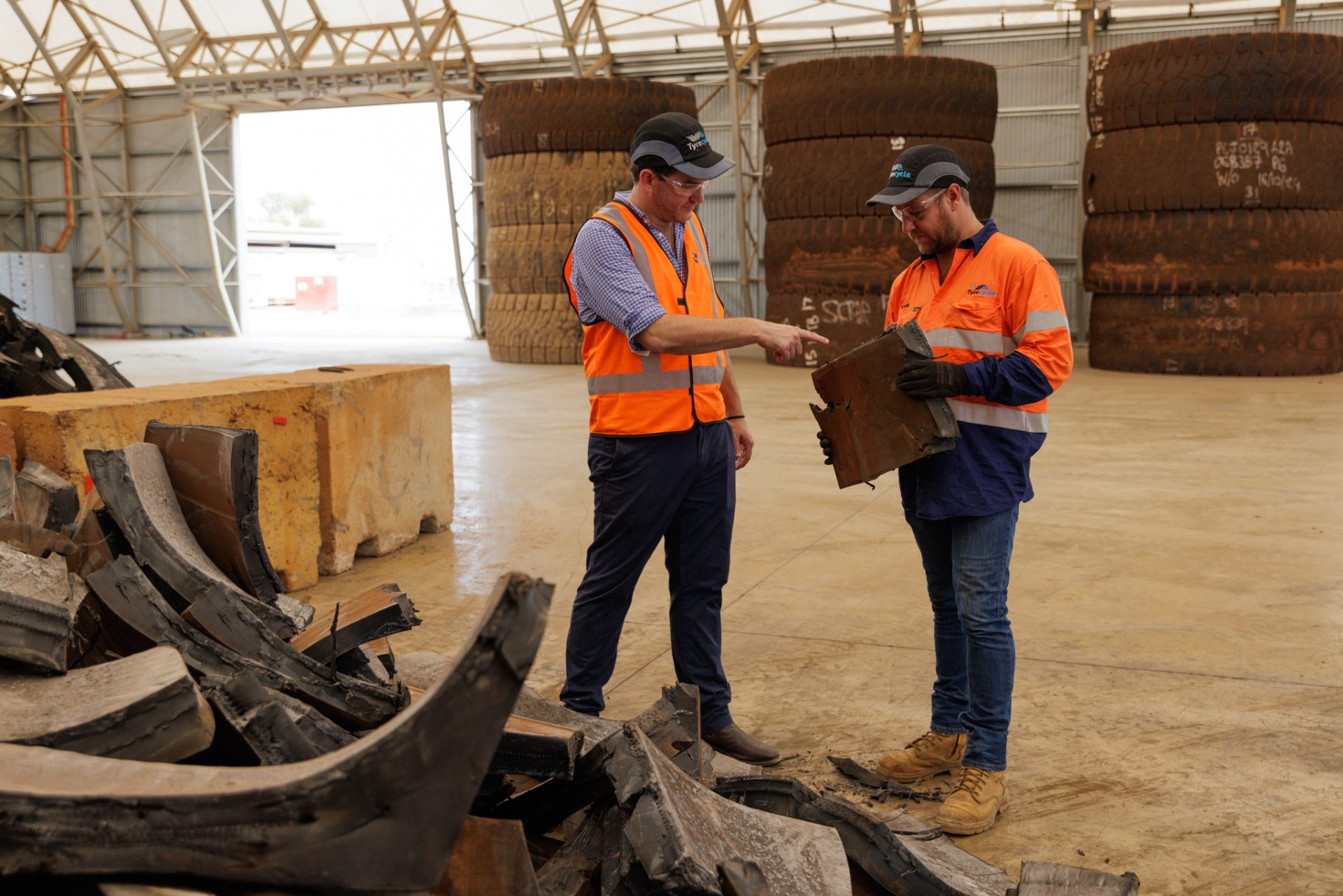
Fairweather believes the new facility will address a significant gap in Australia’s capability of recycling mining tyres.
“We’re collecting OTR tyres at 10%, while mining tyres are only being collected at 1%, so there is a significant shortfall in the market which needs to be addressed,” he said.
“There’s 130,000 tonnes of OTR mining tyres generated every year in Australia and 50,000 tonnes of that is generated in the Pilbara, so if you’re going to build a plant to process these tyres anywhere around the country, you put it in Port Hedland.”
OTR mining tyres will be pre-processed at the Port Hedland facility before being sent to Tyrecycle’s facility in East Rockingham (south of Perth).
Tyrecycle’s East Rockingham site is Australia’s largest and most versatile tyre recycling operation, where OTR mining tyres will be processed into a wide range of products, including crumb rubber, which is used in road development, and our tyre derived fuel, which reduces greenhouse gas emissions by displacing coal as an energy source.